Manufacturing workforce retention: 5 critical company culture action items
Workforce retention plays a big part in growth, innovation, and business continuity for manufacturers. Find out how you can hold on to top talent by improving your company culture.
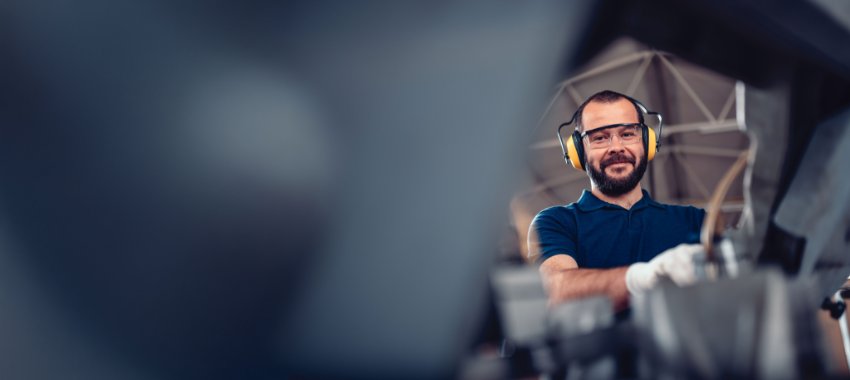
Manufacturing has two big challenges that could impact performance really soon: An aging, fast-retiring workforce and a skills overhaul driven by technology. Decoded, this means they might not have the right people in the right roles at the right times – and it’s not a problem they can easily hire their way out of in the short term. According to the National Association of Manufacturers, 67% of manufacturers cited the inability to attract and retain employees as their top challenge.
The scale of the problem is worth paying attention to. Research from Deloitte and The Manufacturing Institute found 1.9 million manufacturing jobs could be unfilled by 2033 if companies can’t solve these skill and applicant gaps.
We all know ongoing labor shortages are a threat to growth, innovation, and business continuity. But they aren’t inevitable. One powerful tool no one should overlook is culture. The right culture makes top performers want to stay and keeps everyone focused on doing the work they’re meant to do, creating more value for organizations. While the term “culture” can feel nebulous and fuzzy, our new Pulse of Talent research shows that there are clear factors that make a culture great.
Recognize the importance of company culture
Organizational culture can often be treated as a secondary concern. And that’s because it has a reputation for not having serious business impacts. But rethinking that perception is the first step for manufacturers in their journey to build a strong culture.
Consider some of the data that shows the value of culture. For example, 71% percent of CEOs surveyed recently by executive search and advisory firm Heidrick & Struggles highlighted culture as a top factor positively influencing performance – up 26% from 2021.
Our 15th Annual Pulse of Talent survey shows even more evidence for the importance of culture. Among the 995 manufacturing executives, HR leaders, managers, and workers surveyed, 58% said they would or have turned down a job opportunity because the company’s culture didn’t feel like the right fit.
When respondents were asked what a stronger culture would change for them, the top answers were making them feel more engaged (49%), motivating them to work harder (47%), and improving mental health (39%). And manufacturers need an engaged, motivated, and happy workforce to stay competitive in today’s challenging business climate.
To maintain motivation in your organizational culture makeover, keep its value in mind as you progress through the next steps.
Fix the technology gap
Innovation is a cornerstone of culture, and technology powers innovation. But for technology to be a success factor, people need to experience it in the same way, no matter where they sit in an org chart.
And yet, Dayforce research reveals that while 76% of manufacturing executives and 69% of industry HR leaders agreed they have the technology they need to be efficient in their job, this decreases to 44% for workers.
Deloitte reports that manufacturers’ technology budgets are increasing – sitting at 30% of total operating budgets in 2024, up from 23% in 2023. As your organization makes tech investments, ensure that everyone at every level of the organization has the technology they need to be successful. This helps people do their best work and feel less frustrated in their jobs while organizations reap the rewards of greater efficiency and agility.
Focus on learning and development
As manufacturing technology and processes change, so too do the skills workers need. And you don’t want to lose employees once you spend time and money to upskill or reskill them. That makes career development more important than ever in manufacturing.
But among manufacturing workers surveyed in our 15th Annual Pulse of Talent, less than half have received any learning or training opportunities in the past year. Only 24% said they have access to an online learning platform, which can help manufacturers meet employees – especially frontline workers – where they work.
Worker respondents also painted a grim picture of their career development opportunities, with less than one-third (28%) saying they have a career path with their current employer that aligns their career goals.
Workforce retention, business continuity, and building a strong culture can become big challenges for employers when people don’t have the opportunity to grow and pursue their career goals. And when they ignore learning and development, manufacturers risk falling behind and footing the bill for the high cost of turnover and talent sourcing to fill critical skills gaps.
Communication and listening are essential
The very nature of manufacturing operations makes employee communication and listening more complex. What’s decided in the corner office may not make it to the factory floor. And when workers don’t feel connected to their employer, it’s hard to build a high-performing culture.
Manufacturers need to make investments in technology that simplify and streamline communication across the organization. Our survey shows that 74% of manufacturing executives have a centralized place to get information about what’s happening in the company, but that number plummets to 43% of workers. It’s no wonder then that only 24% of workers said they feel very or extremely informed about what’s happening in their company.
Employee listening also needs an overhaul. Regular engagement surveys are essential for understanding the ROI on culture investments. But many manufacturers are currently in the dark when it comes to their employees’ opinions and perspectives. In fact, 29% of the manufacturing workers in our study said they’re never surveyed by their employer.
Benefits can’t be ignored
Company-provided benefits play a big part in worker well-being and in employees doing their best work. And being able to do their best work creates an environment where culture can thrive.
But first, manufacturers need to create an even playing field throughout their organization. Everyone needs benefits that meet their needs. But in our research, 68% of manufacturing executives said their company is good or very good at providing benefits that meet their needs, compared to 39% of workers.
Manufacturers should now work out whether the issue is a lack of worker awareness of benefits or whether the benefits provided truly don’t align with worker needs. If it’s more of the first problem, HR can help resolve this by ensuring everyone in the organization fully understands the breadth of benefits offered. The second issue can be resolved through technology that delivers data-driven insights to support smarter plan design choices that balance costs with employee value and adoption.
Building a strong company culture isn’t just a feel-good initiative, it’s a strategic investment that consistently prioritizes people and fosters their growth. By focusing on these five critical action items, manufacturers can create an environment where employees feel valued, supported, and inspired to stay for the long haul while also driving higher organizational performance.
You may also like:
Ready to get started?
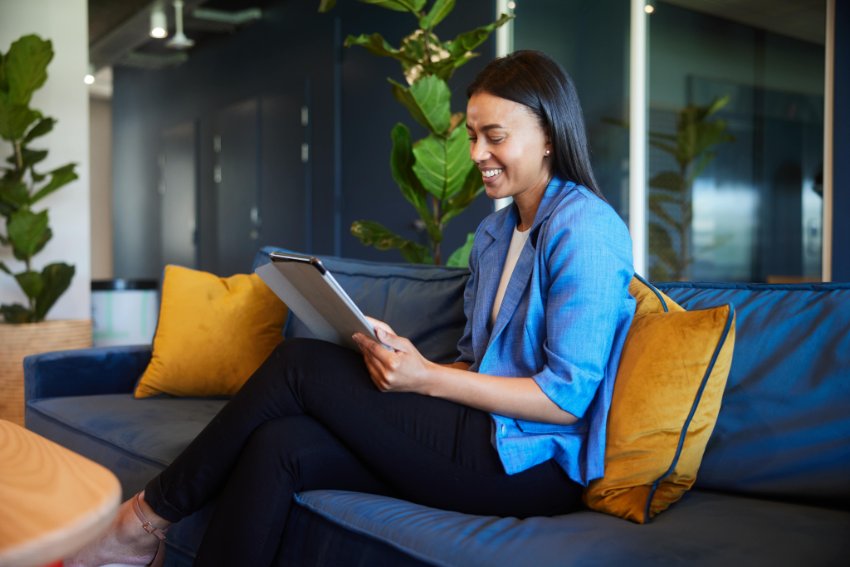