Customer Story
DeRoyal Industries shifts labour and production to supply essential protective equipment

-
3 systems
consolidated into a single solution
-
3 hours
saved on payroll weekly
-
1 person
processing payroll for the entire workforce
Company
Headquarters
Powell, Tennessee, U.S.
Industry
The idea of a family business that starts in a garage and grows to a successful, long-lasting legacy is a familiar dream to many. The entrepreneurial spirit of a young pharmaceutical salesman, Pete DeBusk, took this dream and made it a reality.
DeRoyal Industries was founded 47 years ago, when Pete DeBusk had the idea to develop a shoe to fit over plaster casts to prevent them from being damaged. Since this initial innovation, the company has grown to produce over 25,000 different products, including orthopedic products, surgical and acute care products, unitised delivery systems, and wound care.
Based in Powell, Tennessee, DeRoyal now employs 1,900 people at 21 manufacturing facilities on three different continents. “DeRoyal is somewhat unique in the medical device manufacturing industry now because we're a relatively large company, but we're still family-owned and operated,” says Brian DeBusk, DeRoyal President and CEO and son of founder Pete DeBusk. “Most of the companies that we grew up with in the industry have since been acquired or gone public. But we've chosen to stay a family-owned business. Part of what makes DeRoyal unique is we have a very family-oriented feel.”
It’s this family-oriented culture that has helped the DeRoyal team band together to accomplish great things, especially in the midst of the COVID-19 pandemic.
Shifting production to meet skyrocketing demand
When the COVID-19 pandemic began, DeRoyal noticed a dramatic shift in demand from products for routine procedures to personal protective equipment (PPE). “Instead of a hospital needing 2,000 face shields a week, now they need 2,000 face shields a day,” says DeBusk. “Most estimates have the consumption of personal protective equipment somewhere between 15 to 30 times pre-pandemic levels. So, that was a tremendous shock to the system.”
In response, DeRoyal quickly adapted the material used for the protective eyewear it manufactures to create anti-fog, anti-glare face shields. “The project started in the gym of our corporate building. We recruited volunteers and came up with some basic manufacturing fixtures to produce face shields. We started with 10,000 face shields a week. Before we knew it, we were producing 10,000 face shields a day, then 20,000 a day. And now we peak between 50,000 and 60,000 face shields per day,” says DeBusk.
DeRoyal created portable, low cost face shield manufacturing fixtures – machines designed to produce the face shields – that any employee could operate, then began operating these in the corporate gym, as well as in its manufacturing plants. When a plant had any underutilised labour hours, employees would move from their regular production lines to making face shields. Corporate employees also participated; if their workload was lighter given the current situation, they could assist in production. “When I watch the news and I see the clinician wearing a DeRoyal face shield, I feel we've contributed to the cause and that we’re helping to do what's right for the healthcare workers and for the community to keep everyone safe,” says Karen Clements, DeRoyal’s Vice President of Marketing.
DeRoyal has produced over 800,000 face shields to date, and orders continue to come in daily. “Part of our goal is to produce at such a high rate that our customers feel confident that they can dispose of their single-use PPE equipment because they know there will be more supplied,” says DeBusk.
With this sustained demand, DeRoyal needed to find an efficient, sustainable way to organise its workforce in order to maintain production levels, while ensuring the health and safety of its employees.
Ensuring employee health and safety, and hiring from the community
Given DeRoyal’s classification as an essential business throughout the pandemic, its offices and operations have remained open and employees have continued to manufacture medical equipment.
“Since the products that we make are considered an essential service, we've been fortunate as we haven't had to lay off any employees or cut anyone's hours back. As a matter of fact, we've actually increased employment throughout this pandemic,” says DeBusk.
DeRoyal has been able to hire 60 additional employees to help with the production and assembly of face shields, including furloughed workers from a neighboring business, family and friends of employees who were laid off, and students from a local college who were unable to travel home.
Throughout this increased production, DeRoyal has kept the health and safety of its workforce at the forefront. “It was important to us, even as we made the decision to stay open, that we communicated effectively with our employees about the importance of maintaining a safe work environment and the importance of making sure that we could fulfill our mission of providing this vital personal protective equipment to the customers who counted on us,” says DeBusk.
“Very quickly, our leadership team had to figure out the best way to deploy a remote work plan for office employees and a plan to ensure the health and safety of our manufacturing employees,” says Rebecca Harmon, DeRoyal’s Chief Administrative Officer. DeBusk said that, at the beginning, he did a walk-through of all U.S. facilities to rethink how people were arranged and where there were opportunities to allow for physical distancing between employees. The company also staggered mealtimes, provided employees with masks and protective equipment, and regularly disinfected work areas.
The value of a single system to support HR and payroll continuity
DeRoyal has partnered with Dayforce since 2018, using Dayforce for payroll, time and attendance, recruiting, onboarding, performance, and compensation.
Tracking employee hiring, scheduling, and ensuring that everyone is paid accurately and on time has since become all the more important in light of changing circumstances. “During this time of crisis, paying our employees is a huge priority for the company. I could not imagine going through this process without Dayforce,” says Harmon. “It's a single system that combines time and attendance, HR, and payroll.”
Adds DeBusk, “Dayforce provides us with the platform we need to run the company remotely. So, as the global pandemic hit, our HR function was left completely uninterrupted.”
Dayforce also allows DeRoyal to continue to recruit and onboard new employees remotely as demand for its products continues to grow. “We've continued to recruit and onboard new employees with Dayforce, allowing them to complete the process remotely so that they are not coming into the office,” says Harmon. “It’s certainly created a lot of synergies in our organisation and allowed us to continue to do the same HR functions that we've always done, but in a faster, more secure environment.”
Prior to partnering with Dayforce, DeRoyal had three different systems for HR and payroll functions. With Dayforce, the company was able to consolidate its three separate systems into a single, cloud-based solution that can be accessed from anywhere.
DeRoyal has a single person processing payroll for the entire domestic employee base. Dayforce streamlined components to help them save over 3 hours each week in processing time.
Harmon saw Dayforce as an opportunity to standardise the company’s HR and payroll on a single system, helping DeRoyal ensure every employee got paid the right amount on time. “Dayforce allowed us to consolidate our payroll, which dramatically reduced our administrative costs,” adds DeBusk.
Moving into the new normal
As the pandemic has progressed, companies like DeRoyal have started to think about what the future might hold and how the pandemic will affect industries in the long term.
“It looks like, even after the pandemic subsides, we're probably going to be operating at three to five times run rate for not only face shields and eyewear, but also N95 masks and isolation gowns. I think we're going to dramatically increase our footprint in PPE,” says DeBusk. “I think we're also going to see a huge emphasis in the industry on reshoring or nearshoring any medical products that we consider critical to the U.S. supply chain, including the raw materials to manufacture them.”
With regards to the workforce, DeBusk says that there is going to be a continued focus on safety and health. “If you look at what's important to us for the next three to six to even 18 months, it's the continuity of our business. It's making sure that our workforce is safe. It's making sure that our workforce is paid in a timely and accurate manner. And it's also making sure that we have the infrastructure to work remotely or to make the changes that are necessary as unforeseen circumstances occur.”
Related Customer Stories
Ready to get started?
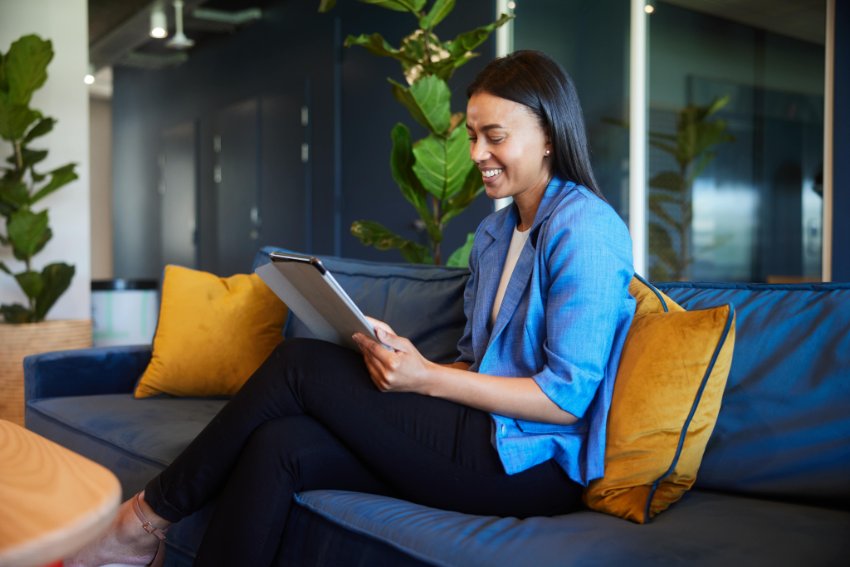