Recruiting as a competitive advantage in manufacturing
Recruiting is a challenge for the manufacturing sectors. Advanced technologies, an aging workforce, and a lack of appeal to the younger workforce are projected to leave almost 2.1 million manufacturing jobs unfilled in the United States alone by 2030. While many recognize that an effective recruiting strategy can be a long-term competitive advantage, few firms are prepared to make the necessary organizational transformation and investments to do so. Here, Matthew Stoll, Managing Principal, Value Advisory at Ceridian, provides perspectives for manufacturers to address these challenges.
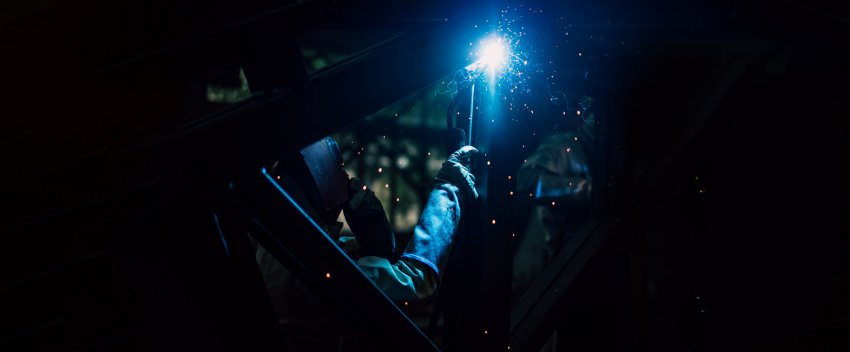
Table of Contents
Advanced technologies, an aging workforce, and a lack of appeal to the younger workforce are projected to leave millions of jobs unfilled in the United States alone in the next decade. While many recognize that an effective recruiting strategy can be a long-term competitive advantage, few firms are prepared to make the necessary organizational transformation and investments to do so. The manufacturing sector would benefit by first recognizing the magnitude of problem and the potential productivity loss due to this labor shortage, and then resolving to address them in three key ways:
- Treat recruiting as an imperative by incorporating and committing to a robust recruiting strategy
- Make continued investments into pertinent education tracts to ensure a strong pipeline of qualified and suitable recruits to meet future skills gaps
- Prepare for and appeal to the future of the manufacturing sector for young people, women, and diverse talent
An inflection point for manufacturers
“Manufacturing is the backbone of a healthy economy” is often touted to recognize the importance of the sector, especially in response to the industry’s decades long decline in employment. And yet, there is a dearth of talent in the manufacturing sector, and a global health crisis has only added to the complexity of this.
The latest report from by Deloitte and The Manufacturing Institute cites that through 2030, there could be as many as 2.1 million unfilled manufacturing jobs in the United States. The potential economic impact from the unfilled positions could be as much as $1 trillion in 2030, according to Deloitte [1]. The same report revealed that the search for skilled talent ranked as the number one driver of competitiveness by manufacturing executives, with 89% of whom agreeing that there is a talent shortage in the U.S. manufacturing sector [2]. As Ceridian’s Vice President of Manufacturing Industry Advisory, Adam Aguzzi observes, “Our customers highlight the search for skilled talent as a critical part of their competitive strategy. Manufacturers all know that it drives their short and long-term business.”
While many organizations have tried to solve for this gap with automation, and/or offshoring, the reality is that those strategies will not be able to cover the industry’s labor demands. Recent labor market data highlights that the industry’s talent shortage challenges are being further compounded by the market’s recovery post-pandemic: while U.S. manufacturing activity hit a 37-year high in March, according to the ISM, the industry has more than half a million job openings [3].
In order to adequately address this critical issue, it is crucial to recognize that the talent shortage in manufacturing is largely driven by three factors:
- Skills gaps: The talent needs of the manufacturing sector are not being met by the current labor market – manufacturers say it’s 36% harder to find talent today than in 2018, according to Deloitte’s report, even with the current higher unemployment rate today [4]
- Aging workforce: About 2.1 million manufacturing jobs will be left unfilled by retirees in the next decade [5]
- Industry and employer brand perception issues: Manufacturing is seen as unappealing to many in the younger generation workforce
Advanced technologies in manufacturing require advanced skills
Manufacturing is often erroneously seen as a low-skilled sector, when in fact, the sector is among the early adherents of the so-called Fourth Industrial Revolution. Manufacturing has been leading the future of work through artificial intelligence, advanced robotics, automation, analytics, and the Internet of Things. A recent McKinsey study describes how the emergence of digitization and automation will require 25% of the global workforce to broaden their technological skills [6]. In fact, the study suggests that the COVID-19 pandemic rewarded manufacturers that have effectively embedded Industry 4.0 technology across its organization, as they responded much better to the crisis [7]. The pandemic has been a wake-up call for late or ineffective adopters of Industry 4.0, recognizing that the largest challenge of implementing the technology is a lack of people, skills, and knowledge, accelerating the search for talent.
Many manufacturing companies are well aware of the industry’s increasing talent gap. In a survey of over 1,200 businesses, almost all respondents say that closing any potential skill gaps is a priority for their organizations [8]. However, among those, only a few indicate that their organizations have adequately responded to those needs. Specifically, 67% of American companies have addressed the emerging skills gap by rapidly hiring, which merely solves for the proximate problem. The talent gap is a progressive crisis, as each passing year compounds the skill demands of the manufacturing sector, following the underlying thesis of Moore’s Law, whereby technology advances exponentially.
Many manufacturing companies have incorporated recruiting into its long-term strategic initiative. Boeing, for example, is investing $285 million in local education and community programs to ensure they have the pipeline of skilled workers needed for its forecasted demand of commercial aircrafts in the next 20 years. It is clear that the most prudent strategy for manufacturing companies to address its skills gap is to simultaneously recruit for its urgent needs, upskill its current workforce, and invest in building up a recruiting pipeline for future needs.
Age and gender: The face of manufacturing needs to change
The manufacturing industry is facing demographic challenges in the next decade. The sector employs one of the oldest workforces. Despite trends among baby boomers to delay retirement – the average age of retirement is now 66, according to a recent Gallup poll [9] – Deloitte predicts that more than 2.6 million baby boomers are expected to retire from manufacturing jobs over the next decade [10].
One of the often-overlooked aspects of this imminent exodus is the amount of tribal knowledge that oils the manufacturing machinery. “The industry understands that there is an urgency driving its recruiting strategy,” says Ceridian’s Aguzzi, Ceridian’s Vice President of Manufacturing Industry Advisory. “Manufacturing is facing a deadline to fill its vacancies as its aging workforce retires en masse, taking knowledge and wisdom that not only drives productivity, but also the operationality of their companies.”
The unkind reality of manufacturing is that the sector has an image problem that makes recruiting particularly difficult. According to Aguzzi, “Recruiting for manufacturing is a challenge because of a lack of sector appeal to the younger generation of the workforce. Millennials don’t find manufacturing ‘attractive,’ somewhat due to the fact that previous generations have too often snubbed their noses at blue collar jobs and pushed their children to pursue ‘more prestigious and lucrative office work.’ To reinforce that point, a different Deloitte survey found that 45% of respondents cited “negative perceptions towards the manufacturing industry” as a cause for the forecasted job vacancies [11].
The good news is that attracting more candidates to manufacturing can be as simple as diversifying the hiring pool and reimagining who wants to work in the space. According to data from the US Census Bureau, women made up just under a third of the manufacturing workforce [12]. The recent Deloitte and The Manufacturing Institute DEI study also revealed a critical gap [13] – while the majority of manufacturing executives feel they’re on a positive track to building an inclusive culture, that sentiment wasn’t matched by the opinions of female, Asian, and Black professionals – respondents in these groups all felt more could be done to create a diverse, equitable, and inclusive environment.
If companies can identify and actively focus on what turns young people and diverse candidates – the future of the industry – off from manufacturing, while fostering growth and inclusion across the organization, then they would put themselves on a better and more valuable track to reap the benefits of a full workforce.
The younger generation desires many things in their career. Often cited is that they value more flexibility and work-life balance than their parents’ generation. But younger workers also simply want personal fulfillment from their careers, and this mindset will carry through as these next-gen workers become our future workplace leaders. “The reality is that the demand for STEM and trade skills is huge,” says Aguzzi. “The right candidates can realize the promise of career positions that are rewarding. Manufacturing can offer the satisfying and fulfilling proposition of building something tangible; we can’t be a global leader existing simply as a service economy.”
Next steps for leaders
Manufacturing leaders must recognize recruiting as an imperative – that incorporating and committing to a robust strategy will be to the organization’s long term, competitive advantage. Secondly, firms need to make prudent investments into communities and educational institutions to ensure that they will have a strong pipeline of qualified and suitable recruits to meet its skills gap. Lastly, organizations must come to terms with the inevitable demographic shift of the manufacturing sector; diverse, next-gen talent is ready to be recruited for these jobs and do the work happily, and productively. In order to do so, companies must be ready to reimagine and then deliver a workplace culture that appeals to the workforce of the future.
[1] Deloitte, Creating pathways for tomorrow’s workforce today: Beyond reskilling in manufacturing, May 2021
[2] Ibid
[3] Matt Egan, CNN, American Factories are desperate for workers. It’s a $1 trillion problem, May 2021
[4] Deloitte, Creating pathways for tomorrow’s workforce today: Beyond reskilling in manufacturing, May 2021
[5] NAM, 2.1 million manufacturing jobs could go unfilled by 2030, May 2021
[6] McKinsey & Company, Closing the future-skills gap, January 2019
[7] McKinsey & Company, Beyond hiring: How companies are reskilling to address talent gaps, February 2020
[8] Gallup, Snapshot: Average American predicts retirement age of 66, May 2018
[9] Deloitte, The jobs are here, but where are the people?, November 2018
[10] Randstad, Manufacturing recruitment: Challenges and opportunities, September 2020
[11] United States Census Bureau, Women in Manufacturing, October 2017
[12] Deloitte, Creating pathways for tomorrow’s workforce today: Beyond reskilling in manufacturing, May 2021
You may also like:
Ready to get started?
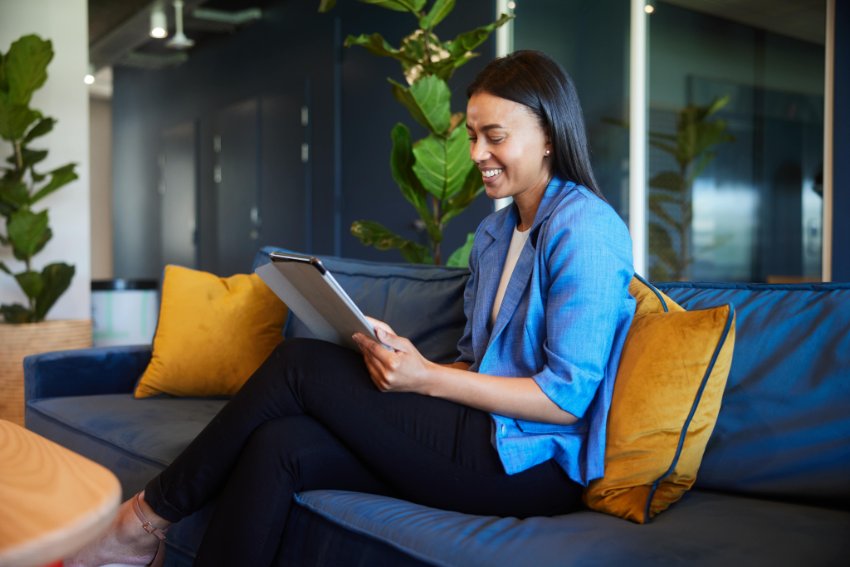