Beyond the headlines: Robots aren’t the biggest threat to the Industry 4.0 workforce
Adam Aguzzi, VP Manufacturing, Value Advisory at Ceridian, outlines three major workforce challenges manufacturers will face as they adapt to Industry 4.0.

There’s a lot going on for manufacturers these days. Some of the headlines surrounding the industry’s rapid technological advancement seem more like Hollywood plotlines than reality. Take the “rise of the machines” narrative, where robots threaten the livelihoods of hardworking people. Or the classic “tale of the underdog,” where companies in emerging markets take down industry giants, leaving a sea of blindsided workers in their wake.
The reality is much more complex – and, in my view, more hopeful. It’s the story of an industry that’s leaning in to the power of technology to drive unprecedented growth, innovation, and transformation. But I’d suggest one major twist: make the workforce the protagonist in the story, not the collateral damage.
The biggest limiting factor to thriving in the Industry 4.0 era may be failing to harness the power of the sector’s greatest asset – people.
Modernizing workforce practices alongside the production line should be a top priority for manufacturers, but achieving this goal is not without its challenges. Every good story has its share of hurdles – here are three for manufacturing leaders to tackle on the road to Industry 4.0 success.
Hurdle #1: Attracting the right people to stay competitive
It’s estimated that 10,000 people retire every day across America, and one quarter of all manufacturing workers are over the age of 55. At the same time, demand for production continues to rise, and the pace of innovation means companies need to act quickly on new market opportunities to stay competitive.
As manufacturing leaders, we need to be thinking ahead about the effects of the aging population on our business. Our organizations risk losing the institutional knowledge retiring experts have accumulated over their long careers, and I fear we will experience a leadership gap without proper succession planning. This applies not only to our management teams, but our “floor leaders” – those in our factories who lead by example.
Getting the right people – especially younger ones – in the door continues to be our biggest challenge as we compete for the same talent. The most in-demand skills of the future – complex problem solving, critical thinking, creativity – are increasingly industry-agnostic, so it’s not just competing for talent in our own lanes.
Our sector also has a branding problem, due in part to misconceptions about our industry: 58% of respondents to a 2018 survey said they believe manufacturing jobs are declining, and only 49% of millennials felt manufacturing could offer them fulfilling careers.
Hurdle #2: Maintaining relevant skills in a rapidly changing context
It’s not enough to simply get people in the door. Contrary to popular belief, there will be plenty of jobs in the manufacturing sector in the future, even if they’ll require different skills than the current workforce holds. Deloitte estimates that the manufacturing skills gap may leave 2.4 million positions unfilled and put $2.5 trillion in manufacturing GDP at risk over the next decade.
This isn’t some vague threat. The high rate of retiring workers coupled with the skills gap is already having a serious negative impact on our organizations, threatening production, limiting innovation, and impairing our companies’ competitive position in the market.
One thing to start on immediately: take action by planning reskilling initiatives, but you may need to approach training differently than you have in the past. The pace of change driven by technology, globalization, and customer expectations shows no signs of slowing, so reskilling can’t be treated as a “one and done” activity. We need to view it as an exercise in continuous improvement.
Hurdle #3: Engaging and retaining employees
We have a lot of catching up to do when it comes to employee engagement. Manufacturing workers are the least engaged employees in the U.S. according to Gallup.
Engagement matters because it has a significant effect on business results: Organizations that score in the top quartile on employee experience report nearly three times the return on assets and double the return on sales of those in the bottom quartile. That is a huge difference, and we as an industry probably need to rethink our approach to managing employees. The old ways of doing things are clearly not working.
Adding to the complexity of engagement is the gap between what millennial and Generation Z employees want from a workplace and what is usually offered. According to Ceridian’s 2018-2019 Pulse of Talent report, they want good benefits (of course) – but they also want training, and to find purpose in their work. Engagement works both ways.
You may also like:
Ready to get started?
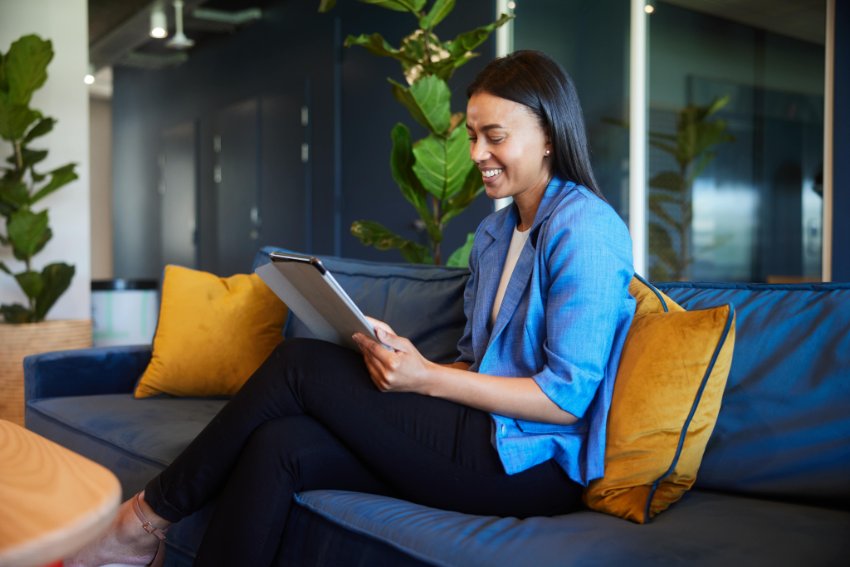