Manufacturing 2020: How to make COVID-19-era workforce agility part of your organization’s permanent DNA
Adam Aguzzi, VP Manufacturing, Value Advisory at Ceridian, explains how perfecting workforce agility now can help your organization adapt and thrive in uncertainty, forever.
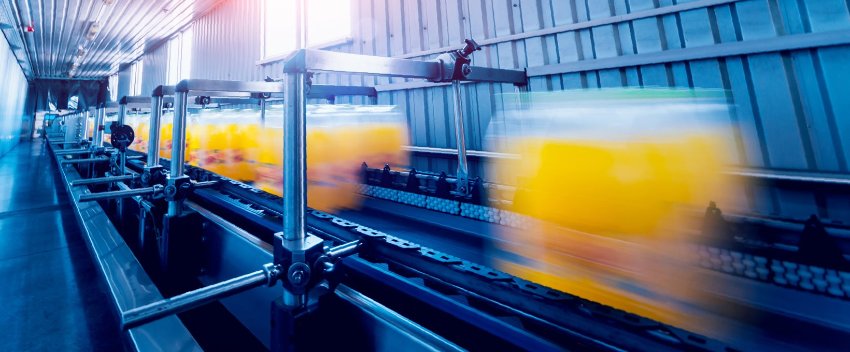
Table of Contents
Table of Contents
The term “agile” has been a popular buzzword for years now. It’s been so overused and misunderstood that some have even declared it dead [1]. But, if we boil it down to its original intention, the term “agile” still means something in manufacturing. It’s about leveraging people’s innate flexibility to adapt processes and respond to change, two concepts that we’ve seen play out in manufacturing during the COVID-19 pandemic.
The pandemic has been one big exercise in agility for the manufacturing sector. It’s easy to think that we’ll eventually settle into a new, calmer reality – except that the manufacturing sector was already operating in a context of constant, rapid change prior to the pandemic, due to the effects of globalization and widespread technology adoption under Industry 4.0. Which means we can either white-knuckle our way through the crisis, or we can use this as an opportunity to make agility part of the sector’s permanent DNA. Organizations that choose the latter will likely have a significant competitive edge, because constant change is the next normal.
Anatomy of an agile manufacturing workforce
According to the article The Relationship Between Work Organization and Workforce Agility in Small Manufacturing Enterprises, in the International Journal of Industrial Ergonomics, there are three pillars of workforce agility: proactivity, adaptability, and resilience [2]. We’re seeing each of these pillars play out right now in real time. Take the 43 workers who lived in the Braskem petrochemical plant in Marcus Hook, Pennsylvania, for nearly a month, working in 12-hour shifts, 24 hours a day, to produce the raw materials needed for PPE [3]. And we’re seeing story after story of companies that pivoted almost overnight to produce medical equipment, or to meet changing consumer demands for food and essential goods – a great example of adaptability and resilience.
In the new reality, the world will continue to change in ways we can’t always predict. Manufacturers will need to prepare the workforce for this prolonged uncertainty, removing the barriers that make it difficult for people to adapt and embrace change. It’s the difference between your workforce driving innovation because it’s who they are, versus being dragged along reluctantly as your competitors define the rules of engagement.
Three lessons on adaptability from the pandemic that we can apply to the broader Industry 4.0 journey
So, what can we learn from the COVID-19 pandemic that will matter later on? As it turns out, a lot. In this article, I’ll explore three key lessons in adaptability that, if you can learn from and solve right now, can help set your workforce and organization up for long-term success.
1. How to maintain production and pivot quickly, even with fewer people
Unemployment is expected to be at around 9% by the end of 2021 [4]. While it marks the end of the historically low joblessness rates that heightened the war for talent over the past few years, it doesn’t spell the end of the shortage of skilled talent manufacturers are facing. For one, the skills gaps predicted before the pandemic – 2.4 million unfilled jobs by 2028 according to Deloitte – will still be an issue [5], as certain technology skills sets remain scarce. At the same time, changes to the global supply chain are poised to create jobs at home, while the “silver tsunami” of retiring workers will reduce the workforce significantly and take away the most experienced workers.
This all compounds to create a situation where manufacturers will likely be operating with fewer people on the line than may be ideal, at least some of the time. While the pandemic is already serving as a dress rehearsal in leaner operations for some essential manufacturers [6], all organizations should be thinking about how to cope with having fewer workers without sacrificing production levels or missing growth opportunities. Doing so requires a “resiliency plan” with the right blend of best practices in business continuity and operational efficiency. An automation strategy alone won’t get you there. Having a plan for your people is critical.
To start, succession planning is critical when facing unpredictability in staffing levels. Succession planning is often considered a leadership development strategy – and it is – but it can also support business continuity. A 2019 joint study by Ceridian and HR Research Institute found that only 20% of HR professionals feel they’re adequately prepared for any employee in a key position to leave [7]. As manufacturers redesign jobs to provide more flexibility, a strong succession plan will include both leader and critical non-manager roles, and it will be integrated with other talent management programs – such as learning and development.
Knowledge management is another critical component to consider. With the impending mass exodus of baby boomers, there’s a significant risk of institutional knowledge and experience heading out the door with them. Organizations will need to digitize their knowledge management and transfer processes to ensure it’s captured for the next generation of the workforce to carry forward. Traditional approaches that just included safety videos and company policies will need to be expanded into upskilling for tomorrow’s needs. Empower workers to take control of their career path and get ready for their next position.
The final piece of the puzzle is building efficiency in systems, processes, and people management. Manufacturers need to examine current digital transformation projects and confirm that workforce management is prioritized. Providing operations managers with visibility to the actual (not standard) costs of every decision in real time will give them a powerful tool to control costs, reduce cost variability, and become both more efficient and predictable. This will never diminish in importance. Given most manufacturers’ second highest expense is labor, it could mean the difference between pivoting profitably or accelerating losses.
2. How to understand and serve the needs of your workforce to gain their loyalty
Perhaps the strongest lesson organizations across all industries can take away from the pandemic is the importance of taking care of your people. During times of crisis, the workforce is judging organizations and leadership teams on how well they steer the ship through the storm. This is especially heightened when stories abound in the news and on social media of organizations going above and beyond to support workers, their families, and the community. This is a time when how you treat your people and the working environment you offer will be under a magnifying glass, and your chosen approach can influence retention – positively or negatively.
One key area of focus is your managers. This layer of the organization plays a critical role in setting the tone and behavior for lower-level employees, and they may find themselves second-guessing their career choices and desiring more stability. Losing managers hurts the culture in the long run, and also has a negative effect on productivity. Failing to support managers through calm leadership, transparent communication, and resources can cause them to lose faith in the company and leave – maybe not right now in the midst of the crisis, but later down the road. The right technology can help foster better business continuity, change management, and self-service, all of which help build managers’ confidence in the organization.
And for the younger generations, working for an organization that cares about its people – and the community – is table stakes. Today’s manufacturers are competing with leading companies in every other industry for millennial and Generation Z talent, especially those with hard-to-recruit tech skills. In one 2018 survey, 58% of respondents said they believe manufacturing jobs are declining, and only 49% of millennials said they believe manufacturing offers fulfilling careers [8]. The pandemic could serve as an opportunity to change the mindset of the younger generations, as manufacturing provides an essential service to communities.
All this being said, major events like the COVID-19 pandemic have a way of changing people’s core values. To truly understand what their workforce needs now – and how that will evolve over the next year or so – organizations will need open, two-way communication. Employee surveys will be more important than ever in helping organizations pivot their approach to the employee experience, over and over, to ensure they can retain the trust and loyalty of their best people.
3. How to rally your people around a purpose – and have them drive change
Going back to the three pillars of workforce agility mentioned at the start of this post, proactivity is the one that may require the biggest culture pivot for manufacturers. Many companies are still using a top-down approach to things like decision-making, problem-solving, and business strategy. This will need to be adjusted to inspire workers at all levels of the organization and across departments to seek out better and more efficient ways of working.
For a workforce to become proactive, they first need to understand what the organization is trying to achieve. Aligning work at all levels back to the company goals is very important, and communicating that vision and strategy clearly even more so. When people feel they’re working toward something they believe in, it can drastically improve performance. In Gallup’s State of the American Workplace report, only four out of 10 employees surveyed strongly agreed that “The mission or purpose of my company makes me feel my job is important” [9]. Gallup suggests that increasing that number to eight out of 10 employees could result in “a 41% reduction in absenteeism and a 33% improvement in quality.”
Manufacturers should consider the role technology can play in communicating, tracking, and measuring progress against goals to keep everyone on the same page within the organization. We’re facing a prolonged period of uncertainty, so change management and transparent communication will be paramount to pivoting quickly and having the workforce drive change.
Moving forward
The COVID-19 crisis has upended every aspect of the reality we knew, but with change comes opportunity. Manufacturers can build a vision that will inspire the workforce to be resilient, embrace change, and solve for the future at every level of the organization. The key is putting the right strategy and technology in place today that will support the workforce in adapting to whatever challenges the future holds.
[1] Kurt Cagle, The end of agile, Forbes, August 2019
[2] Bohdana Sherehiy, Waldemar Karwowski, The relationship between work organization and workforce agility in small manufacturing enterprises, International Journal of Industrial Ergonomics, May 2014
[3] Meagan Flynn, They lived in a factory for 28 days to make millions of pounds of raw PPE materials to help fight coronavirus, The Washington Post, April 2020
[4] Phill Swagel, Updating CBO’s Economic Forecast to Account for the Pandemic, Congressional Budget Office, April 2020
[5] 2018 Skills Gap in Manufacturing Study, Deloitte, 2018
[6] Willem Sundlbad, The Manufacturing Labor Shortage is Still Coming, Stay Prepared, Forbes, April 2020
[7] The State of Succession Management 2019, HR Research Institute and Ceridian, 2019
[8] Manufacturing Index, Leading2Lean, 2018
[9] State of the American Workplace, Gallup, 2018
You may also like:
Ready to get started?
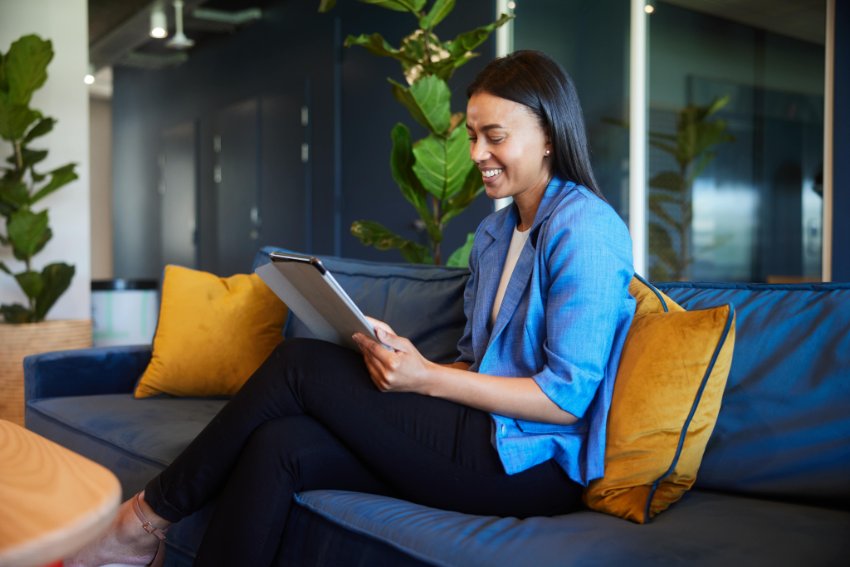