How manufacturing can build a resilient workforce
The manufacturing industry faces a number of challenges, including managing its workforce at a time when workforce shortages are commonplace. Discover several ways that manufacturers can use technology to help enable strategic workforce planning and build a resilient workforce.
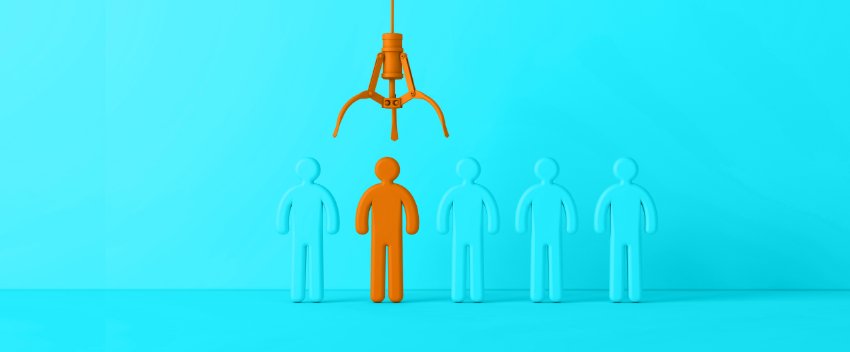
Table of Contents
Unlike many struggling industries, the manufacturing sector has recovered quickly after the pandemic and continues to be one of the top growing industries in the United States. Pent-up demand for consumer products continues to pave the way for continued growth in 2023 and beyond.
Yet, despite these tailwinds, the industry faces a variety of challenges, from ongoing supply chain disruption to navigating digital transformation. Even more important, at a time when labor shortages are commonplace, filling open positions while also retaining existing workers has become an even bigger challenge. Workforce management issues like these impact business continuity for many reasons, especially because of the operational risks they pose for manufacturers.
Solving these workforce issues is critical to keep your workforce productive and competitive while also managing costs. The key is having a sound workforce strategy in place as well as the right underlying technology to support it. Below, we look at several ways manufacturers can use technology for strategic workforce planning to build a more resilient workforce.
1. Empower your people
Organizations that put their people first are fast becoming employers of choice. An important part of doing so is ensuring that the technology your employees use at work is just as convenient and intuitive as the technologies they use in their personal lives. This means adopting technology that’s not only engaging and easy to use, but that also provides real value by giving your people greater control over their schedule, pay, and HR data.
Take scheduling, which is particularly important among today’s workers. According to our Pulse of Talent 2023 survey data, 44% of employees want more flexibility in their schedule. Offering that flexibility is an incredibly powerful way for manufacturers to create an attractive employee value proposition. The best manufacturers empower their employees — whether they’re full-time, seasonal, or gig workers — by providing them more autonomy and control over when they work. Strategic workforce planning tools help you build schedules that meet demand while still giving your workers more flexibility, rather than mandating ineffective schedules that don’t fit into their lives. This way, employees can work the shifts they want and don’t have to adhere to a mandated schedule that may not fit into their life.
Another strategy for empowering your people is meeting them where they are. When you have a deskless workforce, mobile applications allow your people to stay connected while they’re on the go. Your people can easily manage key HR information, see their schedules and pay slips, and receive company communications, all on their phone. Having a great mobile experience can empower your people with more control over their work-life balance and experience at work.
2. Build workforce intelligence
In today’s volatile world, you need systems that help make change easier. Artificial intelligence and machine learning are becoming essential tools to help organizations make data-driven decisions an everyday practice.
After all, even the best planned schedules have to be updated on the fly due to factors ranging from unexpected shifts in demand and employee absences to inclement weather.
A strong workforce management system works alongside people and processes to provide better visibility into labor costs, productivity, and engagement — all while connecting workers. You can increase your organization’s operational agility by making informed staffing decisions based on AI-driven insights.
Your leaders don’t need to be data scientists to achieve success with AI. This level of workforce intelligence is possible when all employee data is on a single platform and easily transformed in personalized dashboards. Not only does access to this kind of intelligence lead to better decisions, it also helps prevent the common delays and inaccuracies that come with integrating employee data from multiple systems.
Alongside materials, equipment, and overhead, labour costs are among manufacturers’ biggest expenses. And they’re steadily on the rise. Without the proper planning systems in place, manufacturers can easily go over budget with unplanned overtime and premium pay for shift workers.
HR teams can control excess labour spend by creating and executing demand-based schedules designed to ensure that they always have the right person in the right place at the right time. Workforce intelligence can help your team leads make better workforce planning decisions that create value for your entire organisation.
3. Upskill efficiently for talent mobility
The skills gap could have devastating consequences. Between a retiring workforce and challenges hiring people with the right skills, this skills gap could result in 2.1 million unfilled manufacturing jobs in the United States by 2030 and potentially costing the industry one trillion.
Your workforce strategy will be more resilient when it’s flexible. More employers are focusing on the essential skills they need to meet organisational goals and nurture high-performing teams. Upskilling and training your existing workers helps them ramp up faster to take on new work instead of spending time and resources hiring and onboarding a new employee.
As a new generation of tech-savvy workers joins the workforce, they also value skills development and internal mobility. Sixty percent of manufacturing respondents in Ceridian’s 2023 Pulse of Talent Survey said they would be more loyal to their employer if they were given opportunities to upgrade their skills.
Employers have a lot to gain by supporting their workers development – better performance at work, improved retention, and a stronger talent pool to encourage internal mobility to react with changing demand.
4. Mitigate risk by staying on top of ever-changing regulatory requirements
Workplace legislation is in a state of constant flux and spans an array of areas, from fair scheduling regulations to union policies, local and national labor laws, and more. An advanced workforce management tool can help limit the chances of running afoul of those requirements and racking up financial penalties as a result. This helps manufacturers mitigate risk across the different regions they operate in.
Payroll is one of the most regulated functions of any organization, with settlements pertaining to wages and hourly compensation becoming a costly compliance issue for most businesses. With the right workforce management system, you can use the latest regulations to govern your scheduling policies, minimize time review cycles, and quickly identify and correct potential errors. This means managing risk and increasing payroll accuracy.
It's time to bolster workforce resiliency with better technology
While the manufacturing industry is poised for a strong future, one of the keys to unlocking that potential is making your workforce more resilient.
With the help of the right workforce management system, you can advance your strategic workforce planning in a way that helps both your employees and your bottom line. For manufacturers, it’s a way to drive employee satisfaction, make better decisions, and manage risk, all while lowering costs. Meanwhile, for employees, it’s a way to have greater control over their schedule and increased access to information.
With an empowered workforce, this sector can better retain frontline workers through fair and flexible schedules built together, rather than mandating ineffective schedules that don’t fit into their lives.
The future of manufacturing is bright. However, going forward, the most successful manufacturers will be the ones that use technology to empower their workforce and their business.
This post was originally published on April 20, 2022 and was updated on June 21, 2023 for recency and to include new perspectives on the topic.
You may also like:
Ready to get started?
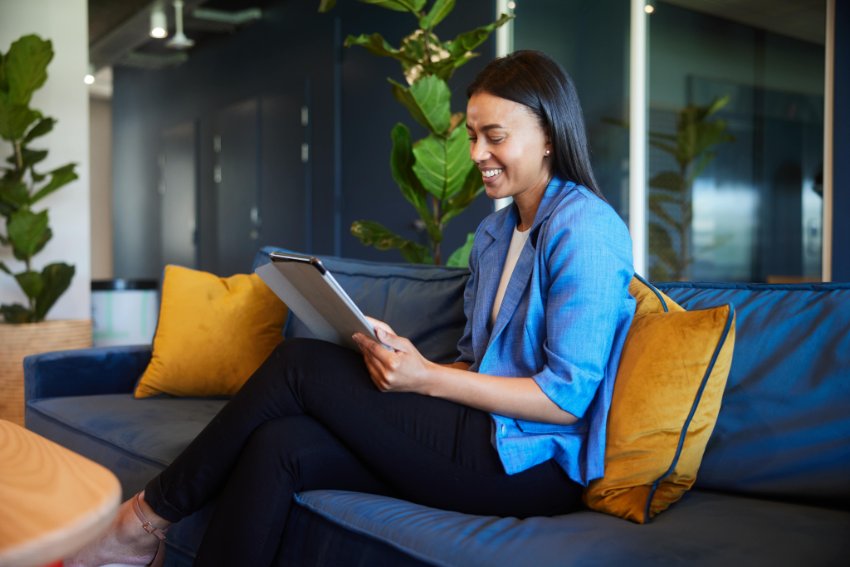